Les stratégies de prévention de la corrosion
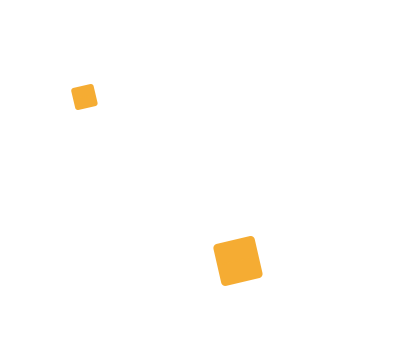
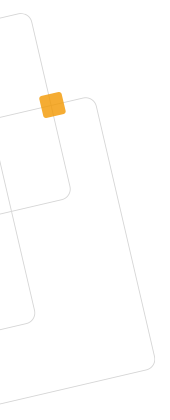
Problème particulièrement onéreux, la corrosion conduit progressivement à la dégradation de matériaux métalliques par réaction chimique avec le milieu qui les environne. Pourtant, les dégâts dus au phénomène de corrosion peuvent généralement être évités en mettant en place quelques mesures simples de prévention anti-corrosion. En effet, différentes stratégies peuvent être utilisées pour limiter la corrosion en intervenant sur le matériel métallique concerné. Découvrez le point complet de nos experts sur les principales stratégies de prévention de la corrosion qui peuvent être mises en place pour améliorer la fiabilité et la durabilité des équipements métalliques.
Protection par revêtement : de multiples stratégies anti-corrosion
Dans le cas de la protection par revêtement, il s’agit de créer une couche protectrice imperméable et inaltérable sur la surface de la pièce métallique à protéger afin d’isoler efficacement le métal de son milieu ambiant. Une étape de préparation de surface est un préalable indispensable à la mise en place de ces moyens de protection contre la corrosion : dégraissage, décapage et, éventuellement, polissage. En plus des revêtements courants comme les peintures et vernis, d’autres types de revêtements ou protections anti-corrosion existent.
Revêtements chimiques
Grâce à une réaction chimique, une couche de sel neutre parfaitement adhérente et imperméable se crée à la surface de la pièce. Selon le métal, différents revêtements chimiques peuvent être employés :
- Phosphatation (pour les métaux ferreux) : immersion des pièces métalliques dans un bain de bioxyde de manganèse et d’acide phosphorique afin d’obtenir une couche protectrice.
- Alodisation (pour les alliages légers) : immersion dans un bain d’alodine pour obtenir une couche protectrice.
- Mordançage (pour les alliages ultra légers) : immersion dans un bain de bichromate de potassium
Revêtements par voie thermique
Ce moyen de prévention contre la corrosion permet de réaliser un dépôt via des métaux protecteurs : étamage (immersion dans un bain d’étain), galvanisation (immersion dans un bain de zinc), aluminage (obtention d’une fine couche d’aluminium)…
Revêtements par dépôt électrolytique
On place à l’anode le métal de protection à déposer (chrome, cuivre, zinc, nickel, …) et à la cathode la pièce métallique à protéger. Sous l’effet du passage du courant, on observe une dissolution de l’anode qui vient recouvrir de métal protecteur la pièce métallique à protéger.
Protection anodique
En plaçant la pièce métallique à protéger à l’anode, en utilisant une cathode en plomb et en plongeant l’ensemble dans un électrolyte, un dégagement d’oxygène se produit à l’anode et une couche protectrice d’oxyde se crée.
Protection cathodique
Utilisée comme prévention d’une corrosion électrochimique, la protection cathodique consiste à éviter la destruction de pièces électronégatives en utilisant des pièces encore plus électronégatives. La cathode présente pourra ainsi se détériorer à la place des pièces métalliques à protéger.
Les tôles galvanisées
La galvanisation à chaud en continu est une opération de revêtement anti-corrosion traditionnelle qui concerne les tôles et les fils revêtus. Ce type de recouvrement est réalisé par immersion au sein d’un bain de zinc (ou d’alliage de zinc) en fusion. En effet, un des atouts majeurs du zinc est sa forte électronégativité comparé à celle de l’acier. Le zinc sert donc de protection électrochimique particulièrement efficace contre la corrosion.
Les vis en inox
Connu particulièrement pour ses propriétés anti-corrosion, l’inox peut écarter efficacement toute substance corrosive grâce à une simple réaction chimique : une couche passive extrêmement fine est formée à la surface par contact entre la composante en chrome de l’inox et l’oxygène contenu dans l’air ou dans l’eau. Les vis en inox sont par conséquent des fixations particulièrement résistantes à la corrosion.
L’anodisation de l’aluminium : une prévention de la corrosion pour l’aluminium
Même s’il est protégé en partie par son oxydation naturelle, l’aluminium soumis à un environnement extérieur peut voir sa surface se ternir progressivement et également se couvrir au fil du temps de piqûres de corrosion. Pour éviter ce phénomène de corrosion atmosphérique, le procédé d’anodisation de l’aluminium (également appelé oxydation anodique) est couramment utilisé. Si de nombreuses techniques sont utilisées (avec acide sulfurique, phosphorique, chromique, oxalique, …), l’anodisation sulfurique reste la plus courante. De façon concrète, la couche d’alumine protégeant naturellement l’aluminium de la corrosion étant très mince et fragile, on utilise ces procédés pour augmenter l’épaisseur de cette couche d’oxyde ainsi que sa résistance.
Le chromage dur : un revêtement anti-corrosion de haute qualité
Egalement efficace pour se prémunir contre la corrosion, le recours au chromage permet d’obtenir une couche superficielle de chrome dur qui se révèle résistant à la majorité des corps chimiques qui attaquent les métaux et surtout à l’oxydation sous l’effet de l’humidité.
Le bain de chrome consiste à tremper la pièce métallique dans un bain où acide chromique et acide sulfurique se trouvent associés. On utilise alors la technique de l’électrodéposition sous courants pulsés. Ce procédé de traitement anti-corrosion permet de déposer du chrome métallique sur la surface à traiter afin de lui conférer les propriétés protectrices de ce métal.
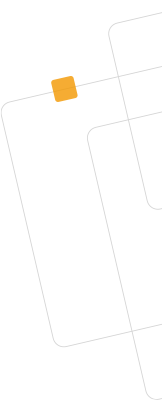